How Can You Accurately Measure an O-Ring?
When it comes to ensuring the integrity and efficiency of mechanical systems, O-rings play a pivotal role. These simple yet essential components are used in a myriad of applications, from automotive engines to household appliances, providing a reliable seal that prevents leaks and maintains pressure. However, the effectiveness of an O-ring hinges on its proper sizing and measurement. If you’ve ever found yourself puzzled over how to measure an O-ring accurately, you’re not alone. Understanding the nuances of O-ring measurement is crucial for anyone involved in engineering, manufacturing, or maintenance.
Measuring an O-ring may seem straightforward, but it involves several critical dimensions that must be taken into account. The inner diameter (ID) and cross-sectional diameter (CS) are the two primary measurements that determine the fit and function of the O-ring in its designated groove. Additionally, factors such as material type and hardness can influence the performance of the O-ring, making accurate measurement even more vital. Whether you’re replacing a worn-out seal or designing a new system, grasping the fundamentals of O-ring measurement will empower you to make informed decisions.
In this article, we will delve into the essential techniques and tools required for precise O-ring measurement. By equipping yourself with this knowledge, you can ensure that your mechanical systems operate smoothly
Understanding O-Ring Dimensions
To accurately measure an O-ring, it is essential to understand its key dimensions, which include the inner diameter (ID), outer diameter (OD), and cross-section or thickness. These measurements are critical for ensuring a proper fit and effective sealing in applications.
- Inner Diameter (ID): The distance across the hole where the O-ring will be seated.
- Outer Diameter (OD): The total distance across the O-ring itself.
- Cross-Section (CS): The thickness of the O-ring, which is the distance from the inner diameter to the outer diameter, divided by two.
Tools Required for Measurement
Accurate measurement of an O-ring can be achieved using several tools. The following items are recommended:
- Caliper: A digital or manual caliper is ideal for measuring the inner and outer diameters accurately.
- Ruler or Tape Measure: For larger O-rings, a flexible tape measure may be useful.
- O-Ring Measuring Gauge: This specialized tool allows for quick and precise measurement of the O-ring dimensions.
Measuring O-Ring Dimensions
To measure an O-ring effectively, follow these steps:
- Measure the Inner Diameter (ID):
- Use the caliper to measure the distance across the inner part of the O-ring.
- Ensure that the caliper jaws are perpendicular to the diameter for an accurate reading.
- Measure the Outer Diameter (OD):
- Position the O-ring on a flat surface.
- Measure across the O-ring from one outer edge to the opposite edge with the caliper.
- Measure the Cross-Section (CS):
- Measure the thickness of the O-ring at its widest point using the caliper.
- This measurement can also be taken from the ID to the OD, divided by two.
Example Measurement Table
The following table illustrates a sample measurement for an O-ring:
Dimension | Measurement (mm) |
---|---|
Inner Diameter (ID) | 10.0 |
Outer Diameter (OD) | 14.0 |
Cross-Section (CS) | 2.0 |
Additional Considerations
When measuring O-rings, consider the following factors:
- Material: Different materials may compress or deform, affecting measurements.
- Temperature: O-ring dimensions can vary with temperature changes; measurements should ideally be taken at room temperature.
- Wear and Tear: If the O-ring is used, wear can alter dimensions, so new O-rings should be measured when possible.
By following these guidelines, you can ensure accurate measurements of O-rings, leading to better performance in sealing applications.
Understanding O-Ring Measurement
Measuring an O-ring accurately is crucial for ensuring proper sealing in various applications. The measurement process involves determining several key dimensions.
Key Measurements for O-Rings
To measure an O-ring effectively, consider the following dimensions:
- Inner Diameter (ID): The distance across the hole or the opening where the O-ring will be placed. This measurement is critical as it dictates the fit within the groove.
- Outer Diameter (OD): The total width of the O-ring from one outer edge to the other. This can be calculated using the formula:
\[
\text{OD} = \text{ID} + 2 \times \text{Cross Section}
\]
- Cross Section (CS): The thickness of the O-ring, essentially the diameter of the circular cross-section. This is a vital measurement that affects compression and sealing capabilities.
Measuring Tools
Utilizing the right tools is essential for accurate measurement. Common tools include:
- Calipers: Digital or manual calipers allow for precise measurements of ID, OD, and CS.
- Micrometers: Ideal for measuring the cross-section of the O-ring with high accuracy.
- Ruler or Measuring Tape: For rough estimates, though not as precise as calipers or micrometers.
Measuring Technique
Follow these steps to ensure accurate measurement:
- For Inner Diameter:
- Use calipers to measure the internal width at the center of the O-ring.
- Ensure the caliper jaws are positioned flat against the inner surface.
- For Outer Diameter:
- Measure from one outer edge to the opposite outer edge using calipers.
- It is essential to take readings at multiple points to account for any irregularities.
- For Cross Section:
- Use a micrometer to measure the thickness of the O-ring at various points.
- Take multiple readings to ensure uniformity in thickness.
Measurement Table Example
Measurement Type | Value (in mm) | Notes |
---|---|---|
Inner Diameter (ID) | 10 | Measure at the widest point. |
Outer Diameter (OD) | 14 | Calculate from ID and CS. |
Cross Section (CS) | 2 | Measure at different points. |
Considerations
When measuring O-rings, keep the following in mind:
- Temperature Effects: O-ring materials can expand or contract with temperature changes, affecting dimensions.
- Material Type: Different materials may have varying tolerances; ensure you are familiar with the specifications of the material being measured.
- Wear and Tear: O-rings that have been in use may have compressed or deformed, so measure the new O-ring for accurate replacement sizing.
By following these guidelines, you can ensure that you measure O-rings accurately for your specific applications, promoting effective sealing and functionality.
Expert Insights on Measuring O-Rings
Dr. Emily Carter (Senior Materials Scientist, Polymer Innovations Inc.). “Accurate measurement of O-rings is crucial for ensuring proper sealing and functionality in various applications. I recommend using calipers to measure the inner diameter, outer diameter, and cross-sectional thickness, as these dimensions directly impact the O-ring’s performance.”
John Thompson (Mechanical Engineer, Sealing Solutions Co.). “When measuring O-rings, it is essential to account for compression and potential deformation. Utilizing a digital caliper provides precision, but also consider measuring the O-ring in its installed position to gauge how it interacts with the housing.”
Linda Martinez (Quality Control Specialist, Industrial Seals Ltd.). “For consistent results, I advise measuring O-rings in a controlled environment to minimize temperature fluctuations. Additionally, documenting measurements in a standardized format helps maintain quality across production batches.”
Frequently Asked Questions (FAQs)
How do I measure the inner diameter of an O-ring?
To measure the inner diameter of an O-ring, use a caliper to measure the distance across the center of the O-ring’s hole. Ensure the caliper is positioned at the widest part of the inner circle for an accurate reading.
What tools are needed to measure an O-ring?
The primary tools required to measure an O-ring include a pair of calipers (digital or manual) for precise measurements, and a ruler or tape measure for larger O-rings if necessary.
How do I determine the cross-sectional diameter of an O-ring?
To determine the cross-sectional diameter, measure the thickness of the O-ring using calipers. Place the calipers perpendicular to the O-ring’s surface and measure the distance across the circular section.
What is the importance of measuring an O-ring accurately?
Accurate measurement of an O-ring is crucial for ensuring a proper fit within its groove, preventing leaks, and maintaining the integrity of the seal in various applications.
Can I use a standard ruler to measure an O-ring?
While a standard ruler can provide a rough estimate, it is not recommended for precise measurements. Calipers are preferred for their accuracy, especially for small diameters and thicknesses.
What should I do if my O-ring is damaged or worn?
If an O-ring is damaged or worn, it is essential to replace it with a new one of the same size and material. Measure the existing O-ring accurately to ensure the new one fits properly and maintains the required sealing properties.
Measuring an O-ring accurately is crucial for ensuring a proper seal in various applications. The process involves determining the O-ring’s inner diameter (ID), outer diameter (OD), and cross-sectional diameter (CS). These measurements can be taken using calipers or specialized O-ring measuring tools. It is essential to follow a systematic approach to obtain precise dimensions, as even minor discrepancies can lead to leakage or equipment failure.
In addition to the basic measurements, it is important to consider the material and hardness of the O-ring, as these factors influence its performance in different environments. Understanding the application requirements, such as temperature, pressure, and chemical exposure, will aid in selecting the appropriate O-ring material and size. Proper storage and handling of O-rings are also vital to maintain their integrity and functionality.
In summary, measuring an O-ring involves careful attention to detail and an understanding of the specific requirements of the application. By following the correct measurement techniques and considering the material properties, one can ensure a reliable seal that meets operational demands. This knowledge is essential for engineers and technicians working in fields where O-rings are commonly utilized.
Author Profile
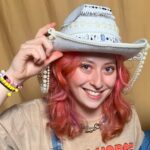
-
A designer by training, a storyteller at heart, and someone who’s always been fascinated by the quiet power of what we choose to wear.
The original Growing Jewelry collection was my attempt to bridge nature and design. I crafted rings that held real moss, asking wearers not just to display them but to care for them.
At first, it was about playfulness and poetry. But as those little green rings made their way into the world, people reached out. And the questions they asked went far beyond moss.
Because jewelry isn’t just sparkle. It’s story, symbol, and self expression and it deserves to be understood as much as admired.
So, if you’ve ever wanted to know why a ruby means passion, or how to keep your silver bright, or what your great-grandmother’s brooch might say about the era she lived in you're in the right place.
Latest entries
- April 18, 2025Investment/ValueHow Much Is a 24K Gold Ring Worth? Unveiling the True Value!
- April 18, 2025Investment/ValueWhat Factors Determine the Cost of a Platinum Ring?
- April 18, 2025MaterialsHow Can You Create Stunning Gold Filled Jewelry at Home?
- April 18, 2025Allergies/SensitivityAre Stainless Steel Earrings Safe for Sensitive Ears?