How Are Rings Made? Unveiling the Secrets Behind Their Creation!
Rings have long been symbols of love, commitment, and personal expression, transcending cultures and generations. From the delicate bands exchanged during wedding ceremonies to the bold statement pieces that adorn fingers, the artistry and craftsmanship behind these circular treasures is as fascinating as the emotions they represent. Have you ever wondered how a simple piece of metal transforms into a stunning ring that captures the essence of a moment or a memory? Join us on a journey through the intricate process of ring making, where creativity meets skill and tradition intertwines with innovation.
The creation of a ring involves a meticulous blend of artistry and technique, beginning with the selection of materials that will ultimately define its character. Jewelers often choose from a variety of metals, gemstones, and finishes, each contributing to the ring’s overall aesthetic and durability. Once the materials are selected, the design process takes center stage, allowing for a unique expression of style and sentiment that reflects the wearer’s personality.
As the crafting process unfolds, various techniques come into play, including forging, casting, and setting. Each method brings its own set of challenges and rewards, requiring a keen eye for detail and a steady hand. From the initial shaping of the metal to the final polishing touches, every step is crucial in ensuring that the finished piece is not only beautiful
Materials Used in Ring Making
The choice of materials is crucial in ring making, as it influences both the aesthetic appeal and durability of the final product. Common materials used include:
- Precious Metals: Gold, silver, and platinum are the most favored due to their luster and resistance to tarnish.
- Alternative Metals: Titanium and tungsten have gained popularity for their strength and lightweight properties.
- Gemstones: Diamonds, sapphires, and emeralds are often set in rings to enhance visual appeal.
- Synthetic Materials: Resins and glass can be used for unique design elements or cost-effective alternatives.
The Ring-Making Process
Creating a ring involves several steps, each contributing to the final piece’s quality and design. Below is an overview of the typical process:
- Design: The initial phase involves sketching the design, determining dimensions, and selecting materials.
- Wax Model Creation: A wax model is often made to visualize the design in three dimensions.
- Casting: The wax model is encased in a mold, and molten metal is poured in to create the ring shape.
- Finishing: The ring undergoes polishing, stone setting, and any necessary engraving to finalize the appearance.
Techniques Employed
Various techniques are utilized in the ring-making process, each offering different aesthetic and structural characteristics:
- Lost Wax Casting: This traditional method allows for intricate designs and fine details.
- Die Striking: Involves stamping metal into shapes, typically used for mass production.
- Hand Fabrication: Artisans manually shape and assemble the ring, providing a unique touch.
Technique | Advantages | Disadvantages |
---|---|---|
Lost Wax Casting | High detail, good for unique designs | Time-consuming, requires skilled artisans |
Die Striking | Efficient for mass production | Limited design flexibility |
Hand Fabrication | Customization and uniqueness | Labor-intensive, more costly |
Quality Control and Finishing Touches
Quality control is a vital step in ring making to ensure that each piece meets industry standards. This includes:
- Inspection for Flaws: Checking for scratches, dents, or imperfections in the metal.
- Stone Security: Ensuring gemstones are securely set and properly aligned.
- Final Polish: Applying a final polish to enhance the shine and remove any minor blemishes.
Each of these steps is essential in delivering a high-quality finished product that meets customer expectations. The care and attention given to the ring-making process significantly impact the overall value and satisfaction of the final piece.
Materials Used in Ring Making
Rings can be crafted from a variety of materials, each influencing the ring’s durability, aesthetic appeal, and cost. The most common materials include:
- Precious Metals
- Gold (available in various karats and colors such as yellow, white, and rose)
- Silver (commonly sterling silver)
- Platinum (known for its density and hypoallergenic properties)
- Palladium (a lighter, more affordable alternative to platinum)
- Alternative Metals
- Titanium (lightweight and strong, ideal for wedding bands)
- Tungsten Carbide (extremely durable and scratch-resistant)
- Stainless Steel (affordable and versatile)
- Gemstones and Other Materials
- Diamonds (most popular choice for engagement rings)
- Other gemstones (sapphires, emeralds, rubies)
- Wood (used in unique, eco-friendly designs)
- Resin (often combined with other materials for artistic effects)
The Ring-Making Process
The production of rings involves several stages, each requiring precision and craftsmanship. The process can vary based on the materials used and the complexity of the design.
- Design
- Conceptual sketches are created, detailing dimensions and features.
- Computer-Aided Design (CAD) software may be utilized for intricate designs.
- Wax Model Creation
- A wax model is crafted based on the design.
- This model helps visualize the final product and serves as a mold.
- Casting
- The wax model is covered in investment material to create a mold.
- The wax is melted away, leaving a cavity for metal.
- Molten metal is poured into the mold, forming the ring.
- Finishing Touches
- The cast ring is cleaned and polished.
- Stones may be set using various techniques such as prong or bezel settings.
- Final polishing ensures the ring has a smooth, reflective surface.
Quality Control in Ring Production
Quality control is essential to ensure that each ring meets industry standards and customer expectations. Key aspects include:
- Material Inspection
- Verification of metal purity and gemstone authenticity.
- Assessment of any alternative materials used for durability and finish.
- Dimensional Accuracy
- Checking the ring size and overall dimensions against specifications.
- Finish Assessment
- Ensuring that the polish and overall aesthetic meet design expectations.
- Examination for any imperfections or flaws.
- Stone Setting Verification
- Confirming that all stones are securely set and aligned properly.
Customization Options
Many jewelers offer customization to meet individual preferences. Common options include:
- Engraving
- Personal messages, dates, or designs can be engraved on the inside or outside of the ring.
- Stone Selection
- Customers can choose specific gemstones, cuts, and arrangements to create a unique look.
- Metal Choice
- Options for different metals or finishes allow for personalized aesthetics.
- Design Alterations
- Modifications to the design can include changes in band width, shape, or style.
Environmental Considerations
Modern ring-making practices increasingly focus on sustainability and ethical sourcing. Considerations include:
- Ethically Sourced Materials
- Ensuring that gemstones and metals are sourced from responsible suppliers.
- Recycled Materials
- Utilizing recycled metals helps reduce environmental impact.
- Eco-Friendly Practices
- Implementing processes that minimize waste and energy consumption during production.
While this section provides a comprehensive overview of how rings are made, it is essential to consult with a jeweler for specific inquiries and to explore further customization options.
Understanding the Craftsmanship Behind Ring Creation
Dr. Emily Carter (Jewelry Design Specialist, Gemstone Journal). “The process of making rings begins with selecting the right materials, which can range from precious metals to alternative materials. Each choice significantly impacts the ring’s aesthetic and durability.”
Michael Tran (Master Goldsmith, Artisan Jewelry Co.). “Crafting a ring involves intricate techniques such as casting, forging, and stone setting. Each method requires a high level of skill and precision to ensure that the final product meets both beauty and structural integrity.”
Laura Kim (Gemologist, Precious Stone Institute). “The selection and placement of gemstones are critical in ring design. Understanding the properties of different stones, including their hardness and refractive qualities, is essential for creating a lasting piece that resonates with the wearer.”
Frequently Asked Questions (FAQs)
How are rings typically made?
Rings are typically made through a process that involves selecting a metal, shaping it into a band, and then adding any desired embellishments such as gemstones or engravings. The primary methods include casting, forging, and machining.
What materials are commonly used to make rings?
Common materials for rings include precious metals such as gold, silver, and platinum, as well as alternative materials like titanium, tungsten, and stainless steel. Gemstones and other decorative elements may also be incorporated.
What is the process of casting a ring?
Casting involves creating a wax model of the ring, which is then coated in a ceramic material. Once the ceramic hardens, the wax is melted away, and molten metal is poured into the mold to create the ring shape.
How are gemstones set in rings?
Gemstones are typically set in rings using various techniques such as prong setting, bezel setting, or channel setting. Each method secures the stone differently, affecting both the aesthetics and security of the gemstone.
What tools are essential for ring making?
Essential tools for ring making include pliers, soldering equipment, a jeweler’s saw, files, and polishing tools. Additional tools may be used depending on the specific techniques employed, such as casting or stone setting.
Can rings be resized, and how is it done?
Yes, rings can be resized by a jeweler through processes such as stretching or cutting and adding metal. The method used depends on whether the ring needs to be made larger or smaller, as well as the design and material of the ring.
Rings are crafted through a meticulous process that combines artistry with engineering. The journey begins with the selection of materials, which can range from precious metals like gold and platinum to alternative materials such as titanium or wood. Each material offers unique properties and aesthetics, influencing the design and durability of the final product. The choice of gemstones, if included, also plays a critical role in the overall appeal and value of the ring.
The manufacturing process typically involves several key steps, including designing, casting, and finishing. Initial designs can be created using traditional sketches or modern CAD software, allowing for precise visualization. Once a design is finalized, the ring is often cast using techniques such as lost-wax casting, which enables intricate details to be captured. After casting, the ring undergoes extensive finishing processes, including polishing, setting stones, and applying any desired textures or engravings, ensuring that the final piece is both beautiful and functional.
In addition to the technical aspects, the emotional significance of rings, particularly in contexts such as engagement and wedding ceremonies, cannot be overlooked. Rings symbolize commitment and love, making their creation not just a craft but a meaningful endeavor. Understanding the craftsmanship behind rings enhances appreciation for these timeless pieces, highlighting the skill and dedication of artisans
Author Profile
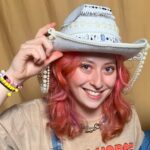
-
A designer by training, a storyteller at heart, and someone who’s always been fascinated by the quiet power of what we choose to wear.
The original Growing Jewelry collection was my attempt to bridge nature and design. I crafted rings that held real moss, asking wearers not just to display them but to care for them.
At first, it was about playfulness and poetry. But as those little green rings made their way into the world, people reached out. And the questions they asked went far beyond moss.
Because jewelry isn’t just sparkle. It’s story, symbol, and self expression and it deserves to be understood as much as admired.
So, if you’ve ever wanted to know why a ruby means passion, or how to keep your silver bright, or what your great-grandmother’s brooch might say about the era she lived in you're in the right place.
Latest entries
- April 18, 2025Investment/ValueHow Much Is a 24K Gold Ring Worth? Unveiling the True Value!
- April 18, 2025Investment/ValueWhat Factors Determine the Cost of a Platinum Ring?
- April 18, 2025MaterialsHow Can You Create Stunning Gold Filled Jewelry at Home?
- April 18, 2025Allergies/SensitivityAre Stainless Steel Earrings Safe for Sensitive Ears?