How Can You Easily Make Your Own O Ring at Home?
How To Make An O Ring?
In the world of engineering and DIY projects, the humble O-ring plays a crucial role in ensuring seals are tight and leaks are nonexistent. Whether you’re working on automotive repairs, plumbing, or even crafting custom machinery, understanding how to make an O-ring can save you time and money while enhancing your skills. This seemingly simple rubber circle is a powerhouse of functionality, providing a reliable barrier against fluids and gases. But how do you create one that meets your specific needs?
Making an O-ring involves more than just cutting a piece of rubber into a circle; it requires knowledge of materials, dimensions, and the intended application. From selecting the right type of elastomer to determining the appropriate size and thickness, each step is vital to achieving the desired performance. As you delve deeper into the process, you’ll discover the various techniques and tools that can help you craft the perfect O-ring for your project.
In this guide, we will explore the fundamentals of O-ring creation, including the materials you can use and the factors that influence their effectiveness. By the end, you’ll have a solid understanding of how to make an O-ring that not only fits your specifications but also stands the test of time in any application. Whether you’re a seasoned professional
Materials Needed
Creating an O-ring requires specific materials that ensure durability and functionality. The choice of material may vary based on the application, but the following are commonly used:
- Rubber: Natural rubber or synthetic options like Nitrile (Buna-N), Neoprene, and Viton.
- Silicone: Excellent for high-temperature applications.
- Polyurethane: Known for its abrasion resistance.
- Teflon: Used for chemically resistant applications.
In addition to materials, other tools and supplies are necessary for the O-ring-making process:
- O-ring cutter or knife
- Measuring tools (calipers or rulers)
- Molding tools (if creating custom shapes)
- Lubricant (for easier installation)
- Safety equipment (gloves and goggles)
Measuring and Cutting
Accurate measurement is crucial when creating O-rings to ensure they fit properly in their intended applications. Follow these steps:
- Determine the Size: Measure the inner diameter (ID) and the cross-section diameter (CS) of the desired O-ring. Common sizes may vary, but for specific applications, referring to industry standards is advisable.
- Cutting the Material: Use an O-ring cutter or a sharp knife to cut the rubber or chosen material. Ensure that the cut is clean and even to facilitate proper sealing.
Here is a simple table summarizing the measurement parameters:
Parameter | Description |
---|---|
Inner Diameter (ID) | Distance across the inside of the O-ring. |
Cross-Section Diameter (CS) | Thickness of the O-ring material. |
Outer Diameter (OD) | Calculated as ID + 2 * CS. |
Joining the Ends
Joining the ends of the O-ring is a critical step that ensures it maintains a seal. There are two primary methods for joining O-ring ends:
- Adhesive Joining: Use a strong adhesive compatible with the O-ring material. Apply the adhesive evenly on both ends and press them together, holding until set.
- Mechanical Joining: This method involves overlapping the ends and securing them with a clamp or similar device, ensuring a tight fit without compromising the O-ring’s flexibility.
Testing and Quality Control
Once the O-ring is assembled, it is essential to test its integrity and suitability for use. Quality control measures may include:
- Visual Inspection: Check for any visible defects or irregularities.
- Pressure Testing: Submerge the O-ring in water or use a pressure chamber to check for leaks.
- Functional Testing: Install the O-ring in its intended application to ensure it meets performance standards.
By meticulously following these steps, you can create an effective and reliable O-ring tailored for specific applications, ensuring optimal performance and longevity.
Materials Required for O-Ring Production
Creating an O-ring necessitates specific materials and tools to ensure quality and performance. Common materials include:
- Elastomers: Typically, materials such as nitrile rubber, fluorocarbon (Viton), silicone, and neoprene are used.
- Steel or Aluminum Rods: For making the cutting tool.
- Cutting Tools: A sharp knife, rotary cutter, or specialized O-ring cutting tool.
- Measuring Tools: Calipers or a ruler for precise measurements.
- Mold (if applicable): For producing O-rings in bulk.
Design Considerations
When designing an O-ring, several factors must be taken into account:
- Diameter: Measure the inner and outer diameters to ensure a perfect fit.
- Cross-Sectional Area: The thickness of the O-ring should correspond to the application requirements.
- Material Selection: Choose the elastomer based on environmental conditions, chemical exposure, and temperature ranges.
Parameter | Description |
---|---|
Inner Diameter | The diameter of the circle formed by the inside edge. |
Outer Diameter | The diameter of the circle formed by the outside edge. |
Cross-Section | The thickness of the ring material. |
Material | Type of elastomer used, e.g., nitrile, silicone. |
Steps to Make an O-Ring
Follow these steps to create a custom O-ring:
- Measure the Required Dimensions: Determine the inner diameter, outer diameter, and desired thickness.
- Select the Material: Choose an appropriate elastomer based on the application.
- Cut the Material: Using a sharp knife or rotary cutter, cut the elastomer to the specified length, ensuring a clean edge.
- Join the Ends:
- For a continuous O-ring, overlap the ends and use a suitable adhesive for the material.
- For a molded O-ring, place the cut material into the mold and cure as per the material specifications.
- Finish the Edges: Smooth out any rough edges to avoid leaks or premature wear.
- Test the O-Ring: Once completed, check the O-ring for fit and functionality in its intended application.
Quality Control Measures
Implementing quality control during O-ring production is crucial. Consider the following measures:
- Dimensional Inspection: Use calipers to verify the inner and outer diameters, ensuring adherence to specifications.
- Material Testing: Conduct tests to assess elasticity, tensile strength, and resistance to chemicals.
- Functional Testing: Test the O-ring in its intended environment to evaluate performance under pressure and temperature.
Applications of O-Rings
O-rings are versatile components used in various industries, including:
- Automotive: Sealing engines, fuel systems, and hydraulic systems.
- Aerospace: Ensuring airtight seals in fuel tanks and pressurized systems.
- Manufacturing: Used in machinery to prevent leaks in hydraulic and pneumatic systems.
- Medical Devices: Ensuring sterile seals in devices and equipment.
By adhering to these guidelines and considerations, one can effectively create high-quality O-rings tailored to specific applications and requirements.
Expert Insights on How to Make an O Ring
Dr. Emily Carter (Materials Scientist, Polymer Innovations Inc.). “Creating an O ring requires precise measurements and the right materials. It’s essential to select a rubber compound that can withstand the specific environmental conditions it will face, such as temperature and chemical exposure.”
Mark Thompson (Mechanical Engineer, SealTech Solutions). “When manufacturing an O ring, ensuring the correct cross-sectional diameter is crucial. This affects the sealing performance and longevity of the ring. Use calipers for accurate measurement and consider the application pressure to determine the optimal size.”
Linda Garcia (Industrial Designer, Precision Seals Co.). “The process of making an O ring can be simplified by using a molding technique. However, attention to detail during the curing process is vital to achieve the desired elasticity and durability, which are critical for effective sealing.”
Frequently Asked Questions (FAQs)
What materials can be used to make an O-ring?
O-rings can be made from various materials, including rubber, silicone, neoprene, and fluorocarbon. The choice of material depends on the application’s temperature, pressure, and chemical compatibility requirements.
What tools are needed to make an O-ring?
To make an O-ring, you will need a cutting tool (such as a sharp knife or O-ring cutter), a measuring tool (like calipers), and a mold if you are using liquid materials. Additionally, a work surface and safety equipment are recommended.
How do you determine the size of an O-ring?
To determine the size of an O-ring, measure the inner diameter (ID) and the cross-sectional diameter (CS) using calipers. The ID is the distance across the inside of the ring, while the CS is the thickness of the material.
Can O-rings be made at home?
Yes, O-rings can be made at home using appropriate materials and tools. However, precision is crucial to ensure a proper seal, so it is essential to measure accurately and cut carefully.
What is the process for making an O-ring?
The process involves selecting the material, measuring the required dimensions, cutting the material to the correct length, and joining the ends using adhesive or by molding, depending on the material used.
Are there specific safety precautions to take when making O-rings?
Yes, safety precautions include wearing gloves to protect against sharp tools, using protective eyewear when cutting materials, and ensuring proper ventilation if using chemicals or adhesives.
making an O-ring involves a series of precise steps that ensure the final product meets the necessary specifications for functionality and durability. The process typically begins with selecting the appropriate material, which can vary based on the intended application and environmental factors. Common materials include rubber, silicone, and fluorocarbon, each offering distinct advantages in terms of temperature resistance, chemical compatibility, and flexibility.
Once the material is chosen, the next step is to determine the correct dimensions for the O-ring. This includes measuring the inner diameter, outer diameter, and cross-section. Accurate measurements are crucial, as even slight deviations can lead to improper sealing and potential failure in applications. After measurements are established, cutting the material to the desired length and joining the ends securely, often through vulcanization or adhesive methods, is essential to create a seamless O-ring.
Finally, testing the O-ring for quality and performance is critical before deployment. This may involve checking for leaks, assessing the fit within the designated groove, and ensuring the O-ring can withstand the operational conditions it will face. By following these steps meticulously, one can successfully create O-rings that provide reliable sealing solutions across various industries.
Key takeaways from the discussion include the
Author Profile
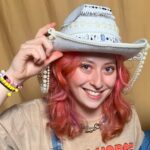
-
A designer by training, a storyteller at heart, and someone who’s always been fascinated by the quiet power of what we choose to wear.
The original Growing Jewelry collection was my attempt to bridge nature and design. I crafted rings that held real moss, asking wearers not just to display them but to care for them.
At first, it was about playfulness and poetry. But as those little green rings made their way into the world, people reached out. And the questions they asked went far beyond moss.
Because jewelry isn’t just sparkle. It’s story, symbol, and self expression and it deserves to be understood as much as admired.
So, if you’ve ever wanted to know why a ruby means passion, or how to keep your silver bright, or what your great-grandmother’s brooch might say about the era she lived in you're in the right place.
Latest entries
- April 18, 2025Investment/ValueHow Much Is a 24K Gold Ring Worth? Unveiling the True Value!
- April 18, 2025Investment/ValueWhat Factors Determine the Cost of a Platinum Ring?
- April 18, 2025MaterialsHow Can You Create Stunning Gold Filled Jewelry at Home?
- April 18, 2025Allergies/SensitivityAre Stainless Steel Earrings Safe for Sensitive Ears?