How Do You Accurately Measure an O-Ring?
Introduction
When it comes to ensuring the integrity of seals and preventing leaks in various applications, O-rings play a crucial role. These simple yet effective components are found in everything from household appliances to complex machinery. However, accurately measuring an O-ring is essential for achieving the perfect fit and optimal performance. Whether you’re a DIY enthusiast tackling a home repair or a professional engineer working on intricate designs, understanding how to measure an O-ring can save you time, money, and frustration. In this article, we will explore the key aspects of O-ring measurement, equipping you with the knowledge needed to select the right size for your specific needs.
To begin with, measuring an O-ring involves two primary dimensions: the inner diameter (ID) and the cross-sectional diameter (CS). The ID is the distance across the hole that the O-ring will fit into, while the CS indicates the thickness of the O-ring itself. Accurate measurements of these dimensions are vital, as even slight deviations can lead to improper sealing and potential failure in applications. Various tools and techniques can be employed to ensure precision, making it essential to choose the right method based on the context of your project.
Additionally, understanding the material properties and tolerances of O-rings is equally important. Different materials offer varying levels
Understanding O-Ring Dimensions
To effectively measure an O-ring, it is essential to understand its key dimensions. The two primary measurements of an O-ring are its diameter and cross-sectional thickness. These dimensions are critical for ensuring a proper fit within a seal groove and effective sealing capabilities.
- Inner Diameter (ID): This is the diameter of the hole that the O-ring fits into. It is measured from the inner edge of the O-ring.
- Outer Diameter (OD): This is the overall diameter of the O-ring, calculated as the sum of the inner diameter and twice the cross-sectional thickness.
- Cross-Sectional Thickness (CS): This dimension refers to the thickness of the O-ring itself and is crucial for determining its sealing capability.
Tools for Measuring O-Rings
To obtain accurate measurements of an O-ring, specific tools are required. The following instruments can be employed for this purpose:
- Calipers: Digital or dial calipers are ideal for measuring the inner and outer diameters as well as the cross-sectional thickness.
- Micrometer: This tool is particularly useful for measuring the cross-section of an O-ring with precision.
- Ruler: A simple ruler can be used for quick measurements but may not provide the accuracy needed for critical applications.
Measuring Process
The process of measuring an O-ring involves several steps to ensure accuracy:
- Inner Diameter Measurement:
- Use calipers to measure the inner diameter directly from the inner edges of the O-ring.
- Cross-Sectional Thickness Measurement:
- Place the O-ring on a flat surface and measure the thickness using calipers or a micrometer at the thickest part of the O-ring.
- Outer Diameter Calculation:
- Once the inner diameter and cross-sectional thickness are known, calculate the outer diameter using the formula:
\[
\text{OD} = \text{ID} + 2 \times \text{CS}
\]
Example of O-Ring Measurement Table
The following table illustrates an example of O-ring measurements for clarity:
Measurement Type | Value (mm) |
---|---|
Inner Diameter (ID) | 20.0 |
Cross-Sectional Thickness (CS) | 2.5 |
Outer Diameter (OD) | 25.0 |
By following these guidelines and utilizing the appropriate tools, accurate measurements of O-rings can be achieved, ensuring proper sealing in various applications.
Understanding O-Ring Dimensions
To accurately measure an O-ring, it is essential to understand its dimensions. O-rings are typically defined by their inner diameter (ID), outer diameter (OD), and cross-section diameter (CS). Each of these measurements plays a crucial role in ensuring a proper fit in applications.
Measuring Inner Diameter (ID)
The inner diameter is the most critical measurement for an O-ring, as it determines how well the O-ring fits over a shaft or into a groove. To measure the ID:
- Use calipers or a precise measuring tool.
- Measure directly across the inner opening from one side to the other.
- Ensure that the O-ring is not twisted or distorted during measurement.
Measuring Outer Diameter (OD)
The outer diameter is calculated based on the inner diameter and the cross-section diameter. However, if measuring directly, follow these steps:
- Lay the O-ring flat on a surface.
- Use calipers to measure across the widest part of the O-ring.
- This measurement provides the outer boundary of the O-ring.
Measuring Cross-Section Diameter (CS)
The cross-section diameter indicates the thickness of the O-ring. This measurement is crucial for ensuring that the O-ring can withstand the pressures and temperatures of the application. To measure the CS:
- Use calipers to measure the thickness of the O-ring at its widest point.
- Ensure that the O-ring is not compressed or deformed during measurement.
Common Measurement Tools
When measuring O-rings, utilizing the appropriate tools is vital for accuracy. Consider the following:
- Vernier Calipers: Ideal for precise internal and external measurements.
- Micrometers: Useful for measuring the cross-section diameter with high accuracy.
- Ruler: Can be used for rough measurements but is less precise than calipers or micrometers.
Standard O-Ring Sizes
O-rings are available in various standard sizes. The following table lists some common sizes:
Inner Diameter (ID) | Cross-Section Diameter (CS) | Common Applications |
---|---|---|
1.78 mm | 1.78 mm | Low-pressure sealing |
2.62 mm | 1.78 mm | Hydraulic systems |
3.53 mm | 2.62 mm | Pneumatic applications |
5.00 mm | 3.53 mm | Automotive applications |
Tips for Accurate Measurement
To ensure that measurements are as accurate as possible, consider the following tips:
- Measure in a controlled environment to avoid variations due to temperature.
- Take multiple measurements and calculate the average to account for any inconsistencies.
- Handle O-rings carefully to avoid deformation, which can lead to inaccurate measurements.
Accurate measurement of O-rings is essential for their effective application in various industries. By following proper measuring techniques and understanding the significance of each dimension, you can ensure that the O-ring will perform its sealing function effectively.
Expert Insights on Measuring O-Rings
Dr. Emily Carter (Materials Scientist, Polymer Research Institute). “To accurately measure an O-ring, one must determine both its inner diameter and cross-sectional thickness. Utilizing calipers for precise measurement is essential, as even minor discrepancies can lead to significant performance issues in sealing applications.”
Michael Thompson (Mechanical Engineer, SealTech Solutions). “When measuring an O-ring, it is crucial to account for the material’s elasticity. A proper measurement involves taking the O-ring out of its groove and measuring it in a relaxed state to avoid any deformation that could affect the size.”
Linda Zhang (Industrial Designer, Sealing Innovations). “For effective measurement of O-rings, I recommend using a dedicated O-ring sizing tool. This not only ensures accuracy but also provides a quick reference for standard sizes, which is invaluable when selecting replacement parts for various applications.”
Frequently Asked Questions (FAQs)
How do you measure the diameter of an O-ring?
To measure the diameter of an O-ring, use a caliper to determine the inner diameter (ID) and outer diameter (OD). The ID is the distance across the inside of the ring, while the OD is the distance across the outside.
What is the correct way to measure the cross-section of an O-ring?
The cross-section of an O-ring is measured by placing it on a flat surface and using a caliper to measure the thickness at the widest point. This measurement is crucial for ensuring a proper fit in its application.
What tools are needed to measure an O-ring accurately?
To measure an O-ring accurately, a digital caliper or a micrometer is recommended. These tools provide precise measurements of both the inner and outer diameters, as well as the cross-section.
Why is it important to measure an O-ring correctly?
Accurate measurement of an O-ring is essential to ensure a proper seal in applications. Incorrect dimensions can lead to leaks, reduced performance, and potential failure of the sealing system.
Can you measure an O-ring without specialized tools?
While specialized tools like calipers provide the best accuracy, you can use a ruler or tape measure for rough estimates. However, this method is not recommended for critical applications where precision is necessary.
What should you do if the O-ring is damaged during measurement?
If an O-ring is damaged during measurement, it is advisable to replace it. A damaged O-ring may not provide a proper seal, leading to potential leaks and system failures.
Measuring an O-ring accurately is crucial for ensuring a proper fit in various applications. The primary dimensions to consider when measuring an O-ring are its inner diameter (ID), outer diameter (OD), and cross-sectional diameter (CS). These measurements can be taken using calipers or specialized O-ring measuring tools. Understanding these dimensions helps in selecting the right O-ring for specific sealing requirements, thereby preventing leaks and ensuring optimal performance.
In addition to the basic measurements, it is essential to consider the material and hardness of the O-ring. Different materials offer varying levels of resistance to temperature, pressure, and chemical exposure. The hardness, often measured on the Shore A scale, affects the O-ring’s ability to compress and create a seal. Therefore, selecting an O-ring with the correct dimensions and material properties is vital for achieving effective sealing in mechanical systems.
Furthermore, when measuring O-rings, it is advisable to account for any deformation that may occur due to compression or wear. This means that the original measurements may differ from those taken after installation. Regular inspection and replacement of O-rings can prevent failures and maintain the integrity of the system. Overall, understanding how to measure an O-ring accurately and selecting the appropriate specifications ensures reliability and longevity in
Author Profile
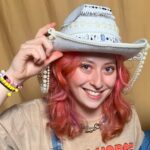
-
A designer by training, a storyteller at heart, and someone who’s always been fascinated by the quiet power of what we choose to wear.
The original Growing Jewelry collection was my attempt to bridge nature and design. I crafted rings that held real moss, asking wearers not just to display them but to care for them.
At first, it was about playfulness and poetry. But as those little green rings made their way into the world, people reached out. And the questions they asked went far beyond moss.
Because jewelry isn’t just sparkle. It’s story, symbol, and self expression and it deserves to be understood as much as admired.
So, if you’ve ever wanted to know why a ruby means passion, or how to keep your silver bright, or what your great-grandmother’s brooch might say about the era she lived in you're in the right place.
Latest entries
- April 18, 2025Investment/ValueHow Much Is a 24K Gold Ring Worth? Unveiling the True Value!
- April 18, 2025Investment/ValueWhat Factors Determine the Cost of a Platinum Ring?
- April 18, 2025MaterialsHow Can You Create Stunning Gold Filled Jewelry at Home?
- April 18, 2025Allergies/SensitivityAre Stainless Steel Earrings Safe for Sensitive Ears?