How Does a Liquid Ring Vacuum Pump Work? Unraveling the Mechanics Behind Its Efficiency
In the world of industrial machinery, efficiency and reliability are paramount, especially when it comes to the management of gases and vapors. Enter the liquid ring vacuum pump—a remarkable device that combines simplicity with effectiveness to create a vacuum environment essential for various applications. Whether in chemical processing, food packaging, or pharmaceuticals, understanding how a liquid ring vacuum pump works can unlock insights into its operational advantages and the integral role it plays in modern manufacturing processes.
At its core, a liquid ring vacuum pump utilizes a rotating mechanism to create a vacuum by trapping and compressing gas within a liquid ring. This ingenious design not only facilitates the removal of air and vapors from a sealed environment but also ensures that the pump operates smoothly and efficiently, minimizing wear and tear. The liquid used in the pump, typically water or oil, serves dual purposes: it acts as a sealing medium and helps to dissipate heat generated during the pumping process.
The versatility of liquid ring vacuum pumps makes them a popular choice across various industries. They are particularly valued for their ability to handle wet and dirty gases without significant performance degradation. As we delve deeper into the workings of this fascinating technology, we will explore its components, operational principles, and the myriad of applications that benefit from its unique capabilities.
Principle of Operation
Liquid ring vacuum pumps operate based on the principle of creating a vacuum by utilizing a rotating impeller and a liquid medium, usually water or oil. The impeller is mounted on a shaft that is eccentric to the pump casing. As the impeller rotates, it generates a liquid ring that forms along the inner wall of the casing. This creates a series of expanding and contracting volumes, effectively drawing in gases and displacing them to create a vacuum.
- The liquid ring acts as a seal, allowing the pump to maintain continuous operation without needing mechanical seals.
- The eccentricity of the impeller causes a variation in volume within the pump, facilitating gas intake and compression.
Components of a Liquid Ring Vacuum Pump
The main components of a liquid ring vacuum pump include:
- Impeller: The rotating part that generates the liquid ring.
- Casing: The housing that contains the impeller and liquid.
- Liquid Reservoir: A supply of liquid that flows into the pump to form the liquid ring.
- Inlet and Outlet Ports: Openings that allow gases to enter and exit the pump.
- Drive Mechanism: Typically an electric motor that powers the impeller.
Component | Description |
---|---|
Impeller | Creates the liquid ring and facilitates gas movement. |
Casing | Houses the impeller and maintains the liquid ring. |
Liquid Reservoir | Supplies the necessary liquid for operation. |
Inlet/Outlet Ports | Allow gas entry and discharge during operation. |
Drive Mechanism | Powers the rotation of the impeller. |
Operational Cycle
The operational cycle of a liquid ring vacuum pump can be divided into several key phases:
- Intake Phase: As the impeller rotates, gas enters the pump through the inlet port, filling the expanding volume formed by the liquid ring.
- Compression Phase: As the impeller continues to rotate, the volume decreases, compressing the gas trapped between the liquid and the impeller.
- Discharge Phase: Once the gas is compressed, it exits through the outlet port, while the liquid returns to the reservoir for recirculation.
This continuous cycle allows for efficient gas handling and vacuum generation, making liquid ring pumps suitable for various industrial applications.
Applications of Liquid Ring Vacuum Pumps
Liquid ring vacuum pumps are widely utilized in numerous industries due to their reliability and efficiency. Common applications include:
- Chemical Processing: For distillation, evaporation, and filtration processes.
- Food and Beverage: In packaging and vacuum cooking.
- Pharmaceuticals: For drying and concentrating products.
- Pulp and Paper: In dewatering processes.
- Vacuum Packaging: To extend the shelf life of products.
Their versatility and ability to handle wet gases without damage make them ideal for these applications.
Principle of Operation
A liquid ring vacuum pump operates based on the principle of creating a low-pressure zone through the rotation of an impeller within a liquid-filled chamber. The liquid, typically water or a compatible oil, forms a ring around the impeller, which plays a crucial role in the pump’s functionality.
- Impeller Design: The impeller features vanes or blades that extend radially, and as it spins, it moves the liquid outward due to centrifugal force.
- Liquid Formation: The liquid forms a ring against the outer wall of the pump casing, creating chambers of varying volume.
- Vacuum Creation: As the impeller rotates, the volume of these chambers increases on one side, causing a drop in pressure and thus generating a vacuum. This allows gases to be drawn into the pump.
Components of a Liquid Ring Vacuum Pump
The primary components of a liquid ring vacuum pump include:
Component | Function |
---|---|
Impeller | Rotates to create liquid motion and vacuum. |
Casing | Houses the impeller and liquid, maintaining the vacuum. |
Liquid Reservoir | Supplies and recirculates the sealing liquid. |
Suction Port | Where gases enter the pump. |
Discharge Port | Where the pumped gases exit, often containing some vaporized liquid. |
Operating Cycle
The operating cycle of a liquid ring vacuum pump can be broken down into several phases:
- Suction Phase: As the impeller rotates, gas enters the pump through the suction port, filling the expanding chambers created by the impeller’s motion.
- Compression Phase: Once the impeller continues to rotate, the volume of the chambers decreases, compressing the gas.
- Discharge Phase: The compressed gas exits through the discharge port. Any liquid mixed with the gas is separated and returned to the reservoir.
Advantages of Liquid Ring Vacuum Pumps
Liquid ring vacuum pumps offer several benefits, making them suitable for various applications:
- Continuous Operation: Capable of operating continuously without significant wear on moving parts.
- Self-Priming: Can handle liquid and vapor mixtures, making them versatile for different processes.
- Low Maintenance: Fewer moving parts lead to reduced maintenance requirements.
- Environmentally Friendly: Minimal emissions, as the liquid can capture contaminants from the gas stream.
Applications
Liquid ring vacuum pumps find extensive use across various industries:
- Food and Beverage: For packaging and processing applications.
- Pharmaceutical: In processes requiring sterile environments.
- Chemical Processing: Useful in distillation and evaporation processes.
- Vacuum Drying: Employed in drying materials without oxidation.
Considerations for Use
When selecting and operating a liquid ring vacuum pump, consider the following factors:
- Type of Liquid: Choose a liquid compatible with the gases being pumped and the environmental conditions.
- Temperature and Pressure: Ensure the pump operates within the specified limits for optimal performance.
- Maintenance Schedule: Regular checks on the liquid level and pump performance can extend the pump’s life.
By understanding these aspects, operators can maximize the efficiency and effectiveness of liquid ring vacuum pumps in various applications.
Understanding the Functionality of Liquid Ring Vacuum Pumps
Dr. Emily Carter (Mechanical Engineer, Vacuum Technology International). “Liquid ring vacuum pumps operate based on the principle of creating a vacuum through the rotation of an impeller within a liquid-filled chamber. The liquid, typically water or oil, forms a ring around the impeller, which helps in trapping gas and creating a low-pressure area. This design is particularly effective for handling vapor and humid gases.”
James Thompson (Process Engineer, Industrial Pump Solutions). “The efficiency of a liquid ring vacuum pump lies in its ability to maintain a consistent vacuum level while minimizing the risk of overheating. The liquid acts as both a sealing medium and a coolant, which is essential for applications that involve high temperatures or corrosive gases. This dual functionality enhances the longevity and reliability of the pump.”
Linda Chen (Vacuum Systems Specialist, Global Engineering Group). “One of the key advantages of liquid ring vacuum pumps is their ability to handle large volumes of gas with varying moisture content. Unlike dry vacuum pumps, they can tolerate liquid carryover without significant performance loss, making them ideal for industries such as food processing and pharmaceuticals, where moisture is often present.”
Frequently Asked Questions (FAQs)
How does a liquid ring vacuum pump operate?
A liquid ring vacuum pump operates by using a rotating impeller within a cylindrical casing. The impeller creates a liquid ring, typically water or oil, which forms a seal. As the impeller rotates, it traps gas in the spaces between the liquid ring and the casing, compressing it and discharging it through an exhaust port.
What are the main components of a liquid ring vacuum pump?
The main components include the pump casing, impeller, liquid ring, suction port, discharge port, and an inlet for the sealing liquid. The impeller is usually mounted on a shaft driven by a motor, and the liquid ring is formed by the centrifugal force of the rotating impeller.
What applications are liquid ring vacuum pumps commonly used for?
Liquid ring vacuum pumps are commonly used in applications requiring low to medium vacuum levels, such as in the chemical, pharmaceutical, food processing, and paper industries. They are also suitable for handling wet or humid gases.
What are the advantages of using a liquid ring vacuum pump?
Advantages include their ability to handle condensable vapors and particulate-laden gases, low maintenance requirements, and the ability to operate in wet environments. They also provide a continuous operation without the risk of overheating.
What types of liquids can be used in a liquid ring vacuum pump?
Water is the most common sealing liquid used, but other liquids such as oils or specialized fluids can be used depending on the application requirements. The choice of liquid affects the pump’s efficiency and the nature of the gases being handled.
How does the efficiency of a liquid ring vacuum pump compare to other types of vacuum pumps?
The efficiency of a liquid ring vacuum pump is generally lower than that of dry vacuum pumps but higher than that of rotary vane pumps in certain applications. Its efficiency is influenced by the design, operating conditions, and the type of sealing liquid used.
A liquid ring vacuum pump operates on a simple yet effective principle that utilizes a rotating impeller to create a vacuum. The pump consists of a cylindrical casing filled with a liquid, typically water or oil, which forms a ring as the impeller spins. This ring of liquid creates a series of chambers that expand and contract, allowing gases to be drawn in and compressed before being expelled. The design is inherently efficient, as it can handle large volumes of gas while maintaining a relatively low operating temperature.
The operation of a liquid ring vacuum pump is characterized by its ability to handle wet and dirty gases, making it suitable for various industrial applications. The liquid used in the pump not only aids in creating the vacuum but also serves as a sealant, preventing gas leaks and ensuring consistent performance. This feature distinguishes liquid ring pumps from other types of vacuum pumps, which may struggle with moisture or particulate matter in the gas stream.
In summary, liquid ring vacuum pumps are versatile and reliable devices that leverage the principles of fluid dynamics to achieve effective vacuum generation. Their unique design allows for efficient gas handling, making them ideal for applications in chemical processing, food production, and wastewater treatment. Understanding the operational mechanics of these pumps is crucial for selecting the appropriate vacuum solution for specific
Author Profile
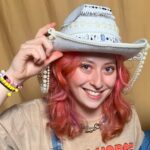
-
A designer by training, a storyteller at heart, and someone who’s always been fascinated by the quiet power of what we choose to wear.
The original Growing Jewelry collection was my attempt to bridge nature and design. I crafted rings that held real moss, asking wearers not just to display them but to care for them.
At first, it was about playfulness and poetry. But as those little green rings made their way into the world, people reached out. And the questions they asked went far beyond moss.
Because jewelry isn’t just sparkle. It’s story, symbol, and self expression and it deserves to be understood as much as admired.
So, if you’ve ever wanted to know why a ruby means passion, or how to keep your silver bright, or what your great-grandmother’s brooch might say about the era she lived in you're in the right place.
Latest entries
- April 18, 2025Investment/ValueHow Much Is a 24K Gold Ring Worth? Unveiling the True Value!
- April 18, 2025Investment/ValueWhat Factors Determine the Cost of a Platinum Ring?
- April 18, 2025MaterialsHow Can You Create Stunning Gold Filled Jewelry at Home?
- April 18, 2025Allergies/SensitivityAre Stainless Steel Earrings Safe for Sensitive Ears?