How Can You Accurately Measure an O Ring?
When it comes to ensuring a perfect seal in various applications, O-rings play a crucial role in preventing leaks and maintaining pressure. Whether you’re working on automotive repairs, plumbing, or industrial machinery, understanding how to measure O-rings accurately is essential for achieving optimal performance. The right fit can mean the difference between a successful project and costly failures. In this article, we will delve into the intricacies of measuring O-rings, equipping you with the knowledge needed to select the perfect size for your needs.
To start, it’s important to recognize that O-rings come in a variety of sizes, materials, and specifications. Measuring them correctly involves more than just grabbing a ruler; it requires a keen understanding of their dimensions, including inner diameter, outer diameter, and cross-section thickness. Each measurement plays a pivotal role in ensuring that the O-ring fits snugly in its designated groove, providing the necessary seal to prevent leaks and ensure efficiency.
Moreover, the process of measuring O-rings can vary depending on the tools available and the specific application at hand. From using calipers for precise measurements to employing simple methods for quick assessments, there are various techniques that can help you achieve accurate results. As we explore these methods further, you’ll gain insights into best
Understanding O-Ring Dimensions
To accurately measure an O-ring, it is essential to understand its key dimensions. The primary measurements you will need to consider are the inner diameter (ID), outer diameter (OD), and the cross-section thickness (CS).
- Inner Diameter (ID): This is the diameter of the hole that the O-ring will fit into. It is a critical measurement as it determines how well the O-ring will seal within the application.
- Outer Diameter (OD): The outer diameter is the total width of the O-ring from one outer edge to the other. It can be calculated from the inner diameter and the cross-section thickness.
- Cross-Section Thickness (CS): This measurement indicates the thickness of the O-ring material itself. The cross-section is vital as it influences the sealing performance and the pressure capabilities of the O-ring.
Measuring Techniques
To measure these dimensions accurately, follow these methods:
- Using Calipers:
- A digital caliper is the most precise tool for measuring O-rings.
- To measure the inner diameter, insert the caliper tips into the hole of the O-ring and read the measurement.
- For the outer diameter, measure across the O-ring from one outer edge to the other.
- For the cross-section, measure the thickness at several points around the O-ring to ensure uniformity.
- Using a Ruler:
- If calipers are not available, a ruler can suffice.
- Place the O-ring on a flat surface and measure the inner and outer diameters carefully.
- For cross-section thickness, place the ruler flat against the O-ring and measure the height.
Measurement Table
A summary table can help visualize the measurements needed for O-ring sizing:
Measurement | Description | Typical Tools |
---|---|---|
Inner Diameter (ID) | Diameter of the hole that the O-ring fits into. | Calipers, Ruler |
Outer Diameter (OD) | Overall diameter of the O-ring. | Calipers, Ruler |
Cross-Section Thickness (CS) | Thickness of the O-ring material. | Calipers, Ruler |
Additional Considerations
When measuring O-rings, consider the following factors that may affect your measurements:
- Material Properties: O-rings can be made from various materials (e.g., rubber, silicone, PTFE), which may have different tolerances and compression characteristics.
- Temperature Effects: The material can expand or contract with temperature changes, potentially altering dimensions slightly.
- Wear and Tear: Used O-rings may have compressed or deformed shapes, leading to inaccurate measurements. It’s best to measure new or undamaged O-rings for precise sizing.
By keeping these aspects in mind, you can ensure accurate measurements of O-rings for effective sealing applications.
Understanding O-Ring Measurements
Measuring an O-ring accurately is crucial for ensuring a proper seal in applications. The key dimensions to consider are the inner diameter (ID), outer diameter (OD), and cross-sectional diameter (CS).
Measuring Inner Diameter (ID)
To measure the inner diameter, follow these steps:
- Use Calipers: Utilize a pair of calipers for precision.
- Position the O-Ring: Place the O-ring on a flat surface.
- Measure: Insert the caliper tips into the inner cavity of the O-ring. Adjust until snug, then read the measurement.
Tip: Ensure that the calipers are perpendicular to the O-ring surface for an accurate measurement.
Measuring Outer Diameter (OD)
The outer diameter can also be measured using calipers:
- Flat Surface: Lay the O-ring flat.
- Caliper Placement: Open the calipers and place one tip at one edge of the O-ring and the other at the opposite edge.
- Read Measurement: Close the calipers gently and read the outer diameter.
Measuring Cross-Sectional Diameter (CS)
The cross-sectional diameter represents the thickness of the O-ring:
- Caliper Measurement: With the O-ring resting flat, use the calipers.
- Measure Thickness: Position one caliper tip on one side of the O-ring and the other tip on the opposite side, then read the measurement.
Measurement Table
Measurement Type | Description | Recommended Tool |
---|---|---|
Inner Diameter | Diameter of the inner cavity | Calipers |
Outer Diameter | Total diameter of the O-ring | Calipers |
Cross-Sectional Diameter | Thickness of the O-ring | Calipers |
Tips for Accurate Measurement
- Temperature: Measure at room temperature, as O-rings can expand or contract with temperature changes.
- Material Consideration: Be mindful of the O-ring material, as some elastomers can deform easily.
- Multiple Measurements: Take several measurements to ensure consistency, especially for larger O-rings.
Additional Considerations
When selecting an O-ring, ensure the following:
- Material Compatibility: Verify that the O-ring material is compatible with the fluids it will contact.
- Application Pressure: Consider the operating pressure and temperature when determining O-ring size.
- Standard Sizes: Familiarize yourself with standard O-ring sizes, which can simplify selection.
Measuring an O-ring involves careful attention to detail. Using calipers for ID, OD, and CS measurements can help in selecting the right O-ring for your application. Regular checks and understanding material properties will enhance performance and reliability.
Expert Insights on Measuring O Rings
Dr. Emily Carter (Senior Materials Scientist, Polymer Innovations Inc.). “Accurate measurement of O rings is crucial for ensuring proper sealing and functionality in various applications. I recommend using calipers for measuring the inner diameter, outer diameter, and cross-sectional thickness to achieve precise dimensions.”
Mark Thompson (Mechanical Engineer, SealTech Solutions). “When measuring O rings, it is essential to account for any deformation that may occur during installation. Using a digital caliper can provide more accurate readings, especially when measuring the cross-section, which is vital for selecting the right replacement.”
Lisa Tran (Product Development Manager, Fluid Dynamics Corp.). “To ensure the longevity and effectiveness of O rings, proper measurement is key. I suggest taking multiple measurements at different points around the O ring to account for any inconsistencies, which can be common in older or worn seals.”
Frequently Asked Questions (FAQs)
How do I measure the diameter of an O-ring?
To measure the diameter of an O-ring, use a caliper to determine the inner diameter (ID) and outer diameter (OD). For the inner diameter, measure the distance across the center of the O-ring’s hole. For the outer diameter, measure the total distance across the O-ring from one edge to the opposite edge.
What tools are needed to measure an O-ring?
A caliper is the most accurate tool for measuring O-rings. A ruler can be used for rough measurements, but a caliper provides precision. Additionally, a micrometer can be used for measuring the cross-section thickness of the O-ring.
How do I measure the cross-section of an O-ring?
To measure the cross-section, use a caliper to measure the thickness of the O-ring at its widest point. Ensure the O-ring is flat and not under any tension during measurement for accurate results.
Why is it important to measure O-rings accurately?
Accurate measurement of O-rings is crucial for ensuring a proper fit in applications, preventing leaks, and maintaining the integrity of seals. Incorrect sizing can lead to premature failure or inadequate sealing.
What is the standard way to specify O-ring sizes?
O-ring sizes are typically specified by their inner diameter and cross-section thickness. For example, a size might be listed as 10mm ID with a 2mm cross-section, which provides essential information for selecting the correct O-ring for a specific application.
Can I use a simple ruler to measure an O-ring?
While a simple ruler can provide a rough estimate, it is not recommended for precise measurements. A caliper is preferred for accurate inner and outer diameter measurements, as well as cross-section thickness.
Measuring an O-ring accurately is crucial for ensuring a proper seal in various applications. The process typically involves determining the O-ring’s inner diameter (ID), outer diameter (OD), and cross-sectional diameter (CS). Using precise tools such as calipers or O-ring measuring tools can facilitate this task, allowing for accurate readings that are essential for selecting the right O-ring for specific applications.
Additionally, understanding the material and hardness of the O-ring is important, as these factors influence its performance and compatibility with different fluids and temperatures. It is also beneficial to consult industry standards and specifications to ensure that the measurements align with the requirements of the intended application.
In summary, measuring an O-ring involves careful attention to detail and the use of appropriate tools. Accurate measurements lead to better sealing performance, which is vital in preventing leaks and ensuring the longevity of the components involved. By following the outlined steps and considering material properties, users can effectively select and implement the right O-ring for their needs.
Author Profile
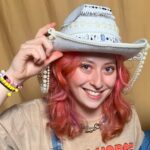
-
A designer by training, a storyteller at heart, and someone who’s always been fascinated by the quiet power of what we choose to wear.
The original Growing Jewelry collection was my attempt to bridge nature and design. I crafted rings that held real moss, asking wearers not just to display them but to care for them.
At first, it was about playfulness and poetry. But as those little green rings made their way into the world, people reached out. And the questions they asked went far beyond moss.
Because jewelry isn’t just sparkle. It’s story, symbol, and self expression and it deserves to be understood as much as admired.
So, if you’ve ever wanted to know why a ruby means passion, or how to keep your silver bright, or what your great-grandmother’s brooch might say about the era she lived in you're in the right place.
Latest entries
- April 18, 2025Investment/ValueHow Much Is a 24K Gold Ring Worth? Unveiling the True Value!
- April 18, 2025Investment/ValueWhat Factors Determine the Cost of a Platinum Ring?
- April 18, 2025MaterialsHow Can You Create Stunning Gold Filled Jewelry at Home?
- April 18, 2025Allergies/SensitivityAre Stainless Steel Earrings Safe for Sensitive Ears?