How Can You Accurately Measure O Ring Size?
When it comes to ensuring a perfect seal in various applications, the importance of selecting the right O-ring size cannot be overstated. Whether you’re a DIY enthusiast tackling a home project or a professional engineer working on intricate machinery, understanding how to measure O-ring size is crucial for achieving optimal performance and longevity. An ill-fitting O-ring can lead to leaks, inefficiencies, and costly repairs, making accurate measurement an essential skill in any toolkit.
Measuring O-ring size involves more than just grabbing a ruler; it requires a keen eye for detail and an understanding of specific dimensions that contribute to the O-ring’s effectiveness. The two primary measurements to consider are the inner diameter (ID) and the cross-section diameter, both of which play pivotal roles in determining how well the O-ring will fit and function within its designated groove. Furthermore, factors such as material type and environmental conditions can influence the choice of O-ring, adding another layer of complexity to the measurement process.
In this article, we will delve into the methods and tools needed to accurately measure O-ring sizes, ensuring that you can select the right component for your needs. From simple techniques that can be performed at home to more advanced approaches used in industrial settings, we will guide you through the essential steps to take the guesswork out of
Understanding O-Ring Dimensions
To accurately measure an O-ring size, it is essential to understand the two primary dimensions: the inner diameter (ID) and the cross-sectional diameter (CS). The inner diameter is the distance across the hole that the O-ring will fit into, while the cross-sectional diameter is the thickness of the O-ring itself.
Tools Required for Measurement
Measuring O-ring size requires specific tools to ensure precision. The following tools are commonly used:
- Caliper: A digital or manual caliper provides accurate measurements for both ID and CS.
- Ruler or Measuring Tape: A flexible ruler can be helpful, particularly for larger O-rings.
- O-Ring Gauge: Specialized tools designed specifically for measuring O-rings can simplify the process.
Measuring the Inner Diameter
To measure the inner diameter of an O-ring, follow these steps:
- Select the Caliper: If using a caliper, ensure it is calibrated.
- Position the O-Ring: Place the O-ring on a flat, stable surface.
- Measure Across the Center: Open the caliper jaws and place them on opposite sides of the inner hole. Note the measurement.
Measuring the Cross-Sectional Diameter
The cross-sectional diameter can be measured as follows:
- Use the Caliper: With the O-ring resting on a flat surface, open the caliper jaws.
- Measure the Thickness: Position the jaws on the thickest part of the O-ring and record the measurement.
Measuring with an O-Ring Gauge
Using an O-ring gauge simplifies the measurement process significantly. The steps are as follows:
- Select the Appropriate Size: Insert the O-ring into the gauge until it fits snugly.
- Read the Size: The gauge will indicate both the inner diameter and cross-sectional size based on the fit.
Measurement Table
The following table provides standard O-ring sizes and their corresponding measurements:
O-Ring Size | Inner Diameter (ID) | Cross-Sectional Diameter (CS) |
---|---|---|
AS568-001 | 0.239 in (6.07 mm) | 0.070 in (1.78 mm) |
AS568-002 | 0.275 in (6.99 mm) | 0.070 in (1.78 mm) |
AS568-003 | 0.364 in (9.24 mm) | 0.070 in (1.78 mm) |
AS568-004 | 0.464 in (11.78 mm) | 0.070 in (1.78 mm) |
Final Considerations
Ensure that measurements are taken with care, as even small discrepancies can affect the performance of the O-ring in its application. When replacing O-rings, it is advisable to refer to manufacturer specifications for the most accurate sizing.
Understanding O Ring Sizes
O rings are essential components in various applications, serving as seals to prevent fluid or gas leakage. The correct sizing is critical to ensure effective sealing and prevent failure in mechanical systems. Measuring the size of an O ring involves determining its inner diameter, outer diameter, and cross-sectional thickness.
Tools Required for Measurement
To accurately measure an O ring, the following tools are recommended:
- Caliper: A digital or dial caliper provides precise measurements of inner and outer diameters.
- Ruler or Measuring Tape: Useful for larger O rings when a caliper may not fit.
- Micrometer: For measuring cross-sectional thickness with high accuracy.
Steps to Measure O Ring Size
- Measure the Inner Diameter:
- Use the caliper to measure the distance across the inside of the O ring at its widest point.
- Ensure the caliper is positioned perpendicular to the ring for an accurate reading.
- Measure the Outer Diameter:
- Place the caliper around the O ring and measure from one outer edge to the opposite outer edge.
- Again, ensure the caliper remains perpendicular to the ring.
- Measure the Cross-Sectional Thickness:
- Use the micrometer to measure the thickness of the O ring at its widest point.
- If a micrometer is not available, a caliper can also be used for this measurement.
Measurement Example
Measurement Type | Value (inches) | Value (mm) |
---|---|---|
Inner Diameter | 0.500 | 12.70 |
Outer Diameter | 0.625 | 15.88 |
Cross-Sectional Thickness | 0.0625 | 1.59 |
Common O Ring Sizes
O rings come in a variety of standard sizes. It is important to reference established sizing charts when selecting replacements. Here are some common sizes:
- AS568A Standard Sizes:
- Dash numbers indicate specific sizes.
- Example: Dash 012 corresponds to an inner diameter of 0.139 inches and a cross-section of 0.070 inches.
Factors to Consider When Measuring
- Material Compression: O rings may compress under pressure; consider the application environment.
- Wear and Tear: An O ring that has been in use may have stretched or compressed, affecting measurements.
- Temperature and Pressure: These factors can alter the size and performance of O rings; ensure measurements are taken in standard conditions.
Using O Ring Size Charts
After obtaining measurements, use O ring size charts to find the closest standard size. These charts provide information on:
- Various materials and their compatible sizes.
- Applications suited for specific O ring dimensions.
- Tolerances and variations based on usage conditions.
Expert Insights on Measuring O Ring Size
Dr. Emily Carter (Mechanical Engineer, SealTech Solutions). “Accurate measurement of O ring size is crucial for ensuring proper sealing and preventing leaks. I recommend using a caliper to measure the inner diameter, outer diameter, and cross-sectional thickness to determine the correct size.”
Mark Thompson (Manufacturing Specialist, Precision Seals Inc.). “When measuring O rings, it is essential to account for any deformation that may occur during installation. Using a digital micrometer can provide precise measurements, which is vital for maintaining the integrity of the seal.”
Linda Garcia (Quality Assurance Manager, Fluid Dynamics Corp.). “For those new to O ring sizing, I suggest referring to industry standards such as AS568. These standards provide detailed specifications and guidelines that can simplify the measurement process and ensure compatibility with various applications.”
Frequently Asked Questions (FAQs)
How do I determine the size of an O-ring?
To determine the size of an O-ring, measure the inner diameter (ID) and the cross-sectional diameter (CS). Use calipers for accurate measurements and refer to standard O-ring size charts for matching dimensions.
What tools do I need to measure an O-ring?
You will need a set of calipers, preferably digital, to measure the inner and cross-sectional diameters. A ruler can also be used for rough measurements, but calipers provide greater accuracy.
Can I measure an O-ring without removing it?
Yes, you can measure an O-ring in place, but it may be challenging. Use calipers to measure the visible portion of the O-ring, ensuring you account for any compression or deformation.
What is the importance of measuring O-ring size accurately?
Accurate measurement is crucial for ensuring a proper seal. An incorrectly sized O-ring can lead to leaks, reduced performance, and premature failure of the sealing application.
Are there standard sizes for O-rings?
Yes, O-rings come in standard sizes defined by industry standards such as AS568. These standards provide a comprehensive list of common O-ring sizes for various applications.
What should I do if I cannot find the exact O-ring size?
If the exact size is unavailable, consider using a slightly larger or smaller O-ring if it fits the application requirements. Alternatively, custom O-rings can be manufactured to meet specific dimensions.
Measuring O-ring size accurately is crucial for ensuring proper sealing and functionality in various applications. The primary dimensions to consider when determining the size of an O-ring are the inner diameter (ID), the outer diameter (OD), and the cross-sectional diameter (CS). To measure these dimensions, one can use calipers for precision, ensuring that the O-ring is not stretched or compressed during the measurement process. It is also important to refer to standard sizing charts that provide information on common sizes and tolerances.
Additionally, understanding the material composition of the O-ring is essential, as different materials can affect the O-ring’s performance in specific environments. Factors such as temperature, pressure, and exposure to chemicals should be considered when selecting the appropriate O-ring size and material. This knowledge aids in preventing leaks and ensuring the longevity of the sealing solution.
measuring O-ring size involves a careful assessment of key dimensions and consideration of material properties. Accurate measurement and selection are vital for achieving optimal sealing performance in any application. By following the outlined steps and utilizing the right tools, individuals can effectively determine the correct O-ring size for their specific needs.
Author Profile
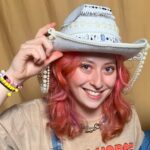
-
A designer by training, a storyteller at heart, and someone who’s always been fascinated by the quiet power of what we choose to wear.
The original Growing Jewelry collection was my attempt to bridge nature and design. I crafted rings that held real moss, asking wearers not just to display them but to care for them.
At first, it was about playfulness and poetry. But as those little green rings made their way into the world, people reached out. And the questions they asked went far beyond moss.
Because jewelry isn’t just sparkle. It’s story, symbol, and self expression and it deserves to be understood as much as admired.
So, if you’ve ever wanted to know why a ruby means passion, or how to keep your silver bright, or what your great-grandmother’s brooch might say about the era she lived in you're in the right place.
Latest entries
- April 18, 2025Investment/ValueHow Much Is a 24K Gold Ring Worth? Unveiling the True Value!
- April 18, 2025Investment/ValueWhat Factors Determine the Cost of a Platinum Ring?
- April 18, 2025MaterialsHow Can You Create Stunning Gold Filled Jewelry at Home?
- April 18, 2025Allergies/SensitivityAre Stainless Steel Earrings Safe for Sensitive Ears?