How Can You Accurately Measure O-Rings for Optimal Performance?
When it comes to ensuring the efficiency and longevity of mechanical systems, the humble O-ring plays a crucial role. These small yet mighty components are essential for creating seals in a variety of applications, from automotive engines to household plumbing. However, to achieve optimal performance, knowing how to accurately measure O-rings is key. Whether you’re replacing an old O-ring or designing a new system, understanding the nuances of O-ring measurement can save you time, money, and frustration.
In this article, we will delve into the essential techniques and tools needed to measure O-rings effectively. From determining the correct diameter to assessing the cross-sectional thickness, each measurement plays a pivotal role in ensuring a proper fit. We’ll explore the different types of O-rings and their applications, highlighting why precision in measurement is critical for achieving reliable seals.
Additionally, we will touch on common pitfalls and best practices to avoid when measuring O-rings. Whether you’re a DIY enthusiast or a seasoned professional, mastering the art of O-ring measurement will empower you to tackle projects with confidence and precision. Get ready to unlock the secrets of this vital component and enhance your understanding of mechanical sealing solutions.
Measuring O-Ring Diameter
To accurately measure the diameter of an O-ring, the first step is to determine its cross-sectional diameter. This is essential as O-rings come in various sizes and specifications. Use a caliper or micrometer for precise measurement. Here’s how:
- Place the O-ring on a flat surface.
- Use the caliper to measure the thickness at several points around the O-ring to ensure accuracy.
- Record the largest value as the cross-sectional diameter.
Next, measure the inner diameter of the O-ring:
- Again, use a caliper to measure from the inside edge of the O-ring.
- Ensure the measurement is taken at multiple points to account for any deformation or wear.
- The inner diameter is crucial for fitting the O-ring into its designated groove.
Measuring O-Ring Size
To determine the size of an O-ring, both the inner diameter and the cross-sectional diameter must be known. The complete size is typically expressed in two dimensions: inner diameter (ID) and cross-section (CS).
For example, if the inner diameter measures 10 mm and the cross-section measures 2 mm, the O-ring size would be represented as 10 x 2 mm.
Here’s a simple table to represent common O-ring sizes:
Inner Diameter (mm) | Cross Section (mm) | Common Size |
---|---|---|
3.0 | 1.0 | 3 x 1 |
5.0 | 1.5 | 5 x 1.5 |
10.0 | 2.0 | 10 x 2 |
20.0 | 3.0 | 20 x 3 |
Measuring O-Ring Groove Dimensions
The groove dimensions where the O-ring will be seated are also critical. An improper groove can lead to O-ring failure, so precise measurements are necessary.
- Width of the Groove: Measure the width of the groove using calipers. This measurement should ideally match the O-ring’s cross-sectional diameter for a snug fit.
- Depth of the Groove: Measure the depth to ensure that the O-ring can sit properly without being overly compressed. A deep groove may lead to O-ring deformation.
- Inner Diameter of the Groove: This should match the inner diameter of the O-ring for optimal sealing.
When documenting these measurements, it is recommended to create a detailed sketch or diagram to illustrate the groove’s dimensions alongside the corresponding O-ring size.
Additional Considerations
When measuring O-rings and their respective grooves, keep the following considerations in mind:
- Material Compression: O-rings can compress under pressure; ensure the measurements account for this.
- Temperature Effects: The material of the O-ring may expand or contract based on temperature, affecting the fit.
- Deformation: If the O-ring has been in use, it may have deformed. Measure it in its resting state if possible.
By following these measurement guidelines, accurate sizes can be obtained, ensuring proper fitting and functionality of the O-rings in their applications.
Understanding O-Ring Dimensions
O-rings are commonly used seals that prevent the passage of fluids or gases. To ensure a proper fit, it is crucial to measure their dimensions accurately. The primary dimensions to consider are the inner diameter (ID), outer diameter (OD), and cross-section diameter (CS).
Measuring Inner Diameter (ID)
To measure the inner diameter of an O-ring, follow these steps:
- Use Calipers: Employ a pair of digital calipers for precise measurement.
- Placement: Open the calipers and place the tips inside the O-ring, ensuring they touch the inner walls.
- Read Measurement: Close the calipers gently until they touch the inner surface, then read the measurement.
Measuring Outer Diameter (OD)
The outer diameter is measured similarly to the inner diameter. Here’s how to do it:
- Caliper Usage: Again, use digital calipers for accuracy.
- Positioning: Place the tips of the calipers around the O-ring.
- Measurement: Close the calipers until they touch the outer surface and read the measurement.
Measuring Cross-Section Diameter (CS)
The cross-section diameter is the thickness of the O-ring. Follow these steps:
- Caliper Technique: Use the calipers to measure the thickness directly.
- Measurement Method: Place the calipers across the O-ring, measuring from one side to the other.
- Ensure Accuracy: Make sure to measure at multiple points to account for any irregularities.
Using a Micrometer for Precision
For even more precise measurements, especially with smaller O-rings, a micrometer can be employed.
- Procedure:
- Open the micrometer and place the O-ring in the measuring area.
- Close the micrometer gently until it just touches the O-ring without compressing it.
- Read the measurement on the micrometer scale.
Measuring Tools Comparison
Tool | Accuracy | Best For |
---|---|---|
Digital Calipers | ±0.01 mm | General purpose |
Micrometer | ±0.001 mm | High precision needs |
Ruler | ±1 mm | Rough measurements |
Considerations for O-Ring Measurement
When measuring O-rings, keep the following in mind:
- Material Deformation: O-rings can deform under pressure. Measure in a relaxed state.
- Temperature Effects: Temperature changes can alter dimensions. Measure at room temperature for consistency.
- Wear and Tear: Old or worn O-rings may not provide accurate measurements. Consider replacing if necessary.
Recording Measurements
It’s advisable to document all measurements for future reference. Use a standardized format:
- ID: [insert measurement]
- OD: [insert measurement]
- CS: [insert measurement]
- Material: [insert material type]
This organized approach facilitates easy comparison and selection when sourcing replacement O-rings.
Expert Insights on Measuring O-Rings
Dr. Emily Carter (Materials Scientist, Polymer Innovations Inc.). “To accurately measure O-rings, one must utilize precise calipers to determine the inner and outer diameters, as well as the cross-sectional thickness. This ensures compatibility with the intended application and prevents potential leaks.”
Michael Chen (Mechanical Engineer, SealTech Solutions). “It is crucial to measure O-rings in a relaxed state, as stretching or compressing them can lead to inaccurate readings. Always take measurements at the O-ring’s resting position for the best results.”
Sarah Thompson (Quality Control Manager, Precision Seals Ltd.). “When measuring O-rings, it is advisable to refer to industry standards such as AS568. This provides a reliable reference for size specifications and helps in selecting the correct O-ring for your application.”
Frequently Asked Questions (FAQs)
How do I determine the size of an O-ring?
To determine the size of an O-ring, measure the inner diameter (ID) and the cross-sectional diameter (CS). Use calipers for accurate measurements, ensuring the O-ring is free of deformation.
What tools are needed to measure O-rings?
A set of calipers, preferably digital for precision, is essential for measuring O-rings. A ruler may also be used for larger O-rings, but calipers provide the best accuracy.
What is the importance of measuring O-rings accurately?
Accurate measurement of O-rings is crucial to ensure a proper fit within the application, which prevents leaks and ensures optimal performance in sealing applications.
Can I measure O-rings without special tools?
While it is possible to use a ruler or tape measure, these methods may lead to inaccuracies. For best results, use calipers to achieve precise measurements.
What are the common sizes of O-rings?
O-rings come in various standard sizes, typically defined by the AS568A standard. Common sizes range from small diameters of 1/16 inch to larger sizes exceeding several inches.
How do I measure the hardness of an O-ring?
To measure the hardness of an O-ring, use a durometer, which provides a reading based on the material’s resistance to indentation. This measurement helps in selecting the right material for specific applications.
Measuring O-rings accurately is crucial for ensuring proper sealing and functionality in various applications. The process involves determining the O-ring’s inner diameter (ID), outer diameter (OD), and cross-sectional diameter (CS). These measurements can be taken using calipers, which provide the precision necessary for selecting the right O-ring for a specific use. Additionally, it is important to consider the material and hardness of the O-ring, as these factors affect its performance under different conditions.
One of the key takeaways from the discussion on measuring O-rings is the significance of using the correct tools and techniques. Calipers, whether digital or manual, offer the best accuracy for measuring the dimensions of O-rings. Furthermore, understanding the tolerances and specifications required for your application is essential to avoid potential leaks or failures. Regularly checking O-ring dimensions can also help in maintaining equipment and preventing costly downtimes.
In summary, measuring O-rings involves a systematic approach to ensure that all dimensions are accurately recorded. Proper measurement techniques not only facilitate the selection of the right O-ring but also contribute to the overall reliability and efficiency of mechanical systems. By adhering to best practices in measurement, users can significantly enhance the performance and longevity of their applications.
Author Profile
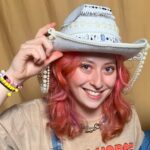
-
A designer by training, a storyteller at heart, and someone who’s always been fascinated by the quiet power of what we choose to wear.
The original Growing Jewelry collection was my attempt to bridge nature and design. I crafted rings that held real moss, asking wearers not just to display them but to care for them.
At first, it was about playfulness and poetry. But as those little green rings made their way into the world, people reached out. And the questions they asked went far beyond moss.
Because jewelry isn’t just sparkle. It’s story, symbol, and self expression and it deserves to be understood as much as admired.
So, if you’ve ever wanted to know why a ruby means passion, or how to keep your silver bright, or what your great-grandmother’s brooch might say about the era she lived in you're in the right place.
Latest entries
- April 18, 2025Investment/ValueHow Much Is a 24K Gold Ring Worth? Unveiling the True Value!
- April 18, 2025Investment/ValueWhat Factors Determine the Cost of a Platinum Ring?
- April 18, 2025MaterialsHow Can You Create Stunning Gold Filled Jewelry at Home?
- April 18, 2025Allergies/SensitivityAre Stainless Steel Earrings Safe for Sensitive Ears?