How Do You Accurately Measure O Rings?
When it comes to ensuring the efficiency and longevity of mechanical systems, the often-overlooked O-ring plays a pivotal role. These small, circular seals are crucial for preventing leaks and maintaining pressure in various applications, from automotive engines to household plumbing. However, to achieve the perfect fit and optimal performance, accurate measurement of O-rings is essential. Whether you’re a DIY enthusiast, a seasoned engineer, or simply curious about the intricacies of sealing technology, understanding how to measure O-rings can save you time, money, and frustration. In this article, we will guide you through the essential techniques and tools needed to measure O-rings effectively, ensuring you get the right size for your specific needs.
Measuring O-rings may seem straightforward, but precision is key to their functionality. The process typically involves determining two critical dimensions: the inner diameter (ID) and the cross-sectional diameter (CS). These measurements ensure that the O-ring fits snugly within its groove, providing the necessary sealing capabilities. Additionally, factors like material type and environmental conditions can influence the choice of O-ring, making accurate measurement even more important.
In the world of O-rings, a small miscalculation can lead to significant issues, including leaks and equipment failure. Therefore, using
Measuring the Inner Diameter
To accurately measure the inner diameter of an O-ring, you can use a caliper or an inside diameter gauge. The inner diameter is crucial because it determines how well the O-ring will fit onto a shaft or in a groove. Follow these steps for precise measurement:
- Place the O-ring on a flat, hard surface.
- Open the caliper’s jaws and gently insert them into the center of the O-ring.
- Close the jaws until they touch the inner wall of the O-ring.
- Read the measurement displayed on the caliper.
For best results, take multiple measurements at different points around the O-ring to account for any irregularities.
Measuring the Outer Diameter
The outer diameter measurement is essential for understanding the overall size of the O-ring. To measure the outer diameter:
- Lay the O-ring flat on a surface.
- Using a caliper, measure the distance across the O-ring, ensuring the caliper’s jaws are touching the outer edges.
- Record the measurement.
It is advisable to take several measurements and average them to ensure accuracy.
Measuring the Cross-Sectional Diameter
The cross-sectional diameter is critical for determining the thickness of the O-ring. This measurement affects the O-ring’s sealing capability. To measure the cross-sectional diameter:
- Place the O-ring flat on a surface.
- Use the caliper to measure the thickness by placing one jaw on the bottom and the other on the top of the O-ring.
- Record the measurement.
Repeat this process at different points to ensure uniformity.
Measuring with a Template
If calipers are not available, a template can be used to measure O-rings. A template can be created using a piece of cardboard or plastic with circular cutouts of various sizes.
- Place the O-ring over the cutouts.
- Identify the cutout that best matches the O-ring’s inner and outer diameters.
- This method provides a quick reference but may lack precision compared to calipers.
Measurement Reference Table
Below is a reference table that outlines the key measurements for O-rings.
Measurement Type | Purpose | Tools Required |
---|---|---|
Inner Diameter | Ensures proper fit onto a shaft or in a groove | Caliper, Inside diameter gauge |
Outer Diameter | Determines overall size | Caliper |
Cross-Sectional Diameter | Affects sealing capability | Caliper |
Template Measurement | Provides quick size reference | Cardboard/Plastic template |
By following these methods, you can ensure accurate measurements of O-rings for various applications. Proper measurement is essential for achieving optimal sealing performance.
Understanding O Ring Dimensions
O rings are characterized by two primary dimensions: the inner diameter (ID) and the cross-sectional diameter (CS). Accurate measurement of these dimensions is crucial for ensuring a proper fit within their designated grooves.
- Inner Diameter (ID): This is the distance measured across the inside of the O ring, from one inner edge to the other.
- Cross-Sectional Diameter (CS): This measurement refers to the thickness of the O ring, taken perpendicular to the inner diameter.
Tools Required for Measurement
To measure O rings accurately, the following tools are recommended:
- Caliper: A digital or dial caliper provides precise measurements for both ID and CS.
- Ruler or Tape Measure: Useful for larger O rings, but less precise than a caliper.
- Micrometer: Particularly effective for measuring cross-sectional diameter, especially for small O rings.
Step-by-Step Measurement Process
Measuring an O ring involves a systematic approach to ensure accuracy:
- Clean the O Ring: Remove any dirt or debris from the O ring’s surface to avoid incorrect measurements.
- Measure the Inner Diameter:
- Open the caliper jaws and place them inside the O ring.
- Gently close the jaws until they touch the inner edge of the O ring.
- Read the measurement displayed on the caliper.
- Measure the Cross-Sectional Diameter:
- Use the caliper to measure the thickness of the O ring by placing the jaws perpendicular to the ring’s surface.
- Ensure a firm yet gentle grip to avoid deforming the O ring.
- Record the measurement.
Measuring Tips for Accuracy
To enhance measurement accuracy, consider the following tips:
- Avoid Stretching: Do not stretch the O ring while measuring, as this can lead to inaccurate readings.
- Use Proper Calibration: Ensure your measuring tools are calibrated correctly before use.
- Multiple Measurements: For larger O rings, take multiple measurements at different points to account for any variations in the material.
Common O Ring Sizes
O rings come in various sizes and standards. Below is a table of common O ring sizes based on the AS568 standard:
AS568 Size | Inner Diameter (ID) | Cross-Sectional Diameter (CS) |
---|---|---|
001 | 0.039 inches | 0.014 inches |
002 | 0.070 inches | 0.014 inches |
003 | 0.103 inches | 0.014 inches |
004 | 0.139 inches | 0.014 inches |
005 | 0.139 inches | 0.024 inches |
Conclusion on Measurement Techniques
Employing the correct tools and methodologies ensures precise measurements of O rings. Ensuring the appropriate fit contributes significantly to the effectiveness of sealing applications across various industries. By adhering to the standards and best practices outlined, one can achieve reliable results when measuring O rings.
Expert Insights on Measuring O Rings
Dr. Emily Carter (Materials Scientist, Polymer Research Institute). “To accurately measure O rings, one must consider both the inner diameter and the cross-sectional thickness. Utilizing calipers can provide precise measurements, but it is crucial to ensure that the O ring is not deformed during the process.”
James Liu (Mechanical Engineer, SealTech Solutions). “When measuring O rings, it is essential to account for the material’s elasticity. I recommend using a digital caliper for the most accurate readings, as it minimizes the risk of human error and provides consistent results.”
Maria Gonzalez (Quality Control Specialist, Industrial Seals Corp). “In my experience, measuring O rings should also include a check for any wear or damage. This can affect the effectiveness of the seal. Always measure multiple points along the O ring to ensure uniformity.”
Frequently Asked Questions (FAQs)
How do I measure the inner diameter of an O-ring?
To measure the inner diameter of an O-ring, use calipers to determine the distance across the center of the ring, ensuring you measure at the widest part for accuracy.
What is the best method to measure the cross-section of an O-ring?
The cross-section can be measured using calipers or a micrometer. Place the O-ring flat and measure the thickness at its widest point to obtain the cross-sectional diameter.
Can I use a ruler to measure O-rings?
While a ruler can be used, it is less precise than calipers. Ensure the ruler is marked in millimeters or inches for accurate readings, and measure carefully to avoid parallax errors.
What tools are recommended for measuring O-rings?
Recommended tools include calipers (digital or manual), micrometers, and O-ring measuring gauges. These tools provide the precision needed for accurate measurements.
How do I determine the size of an O-ring if I do not have measuring tools?
If measuring tools are unavailable, compare the O-ring to a known size or use a template with standard sizes to estimate the diameter and cross-section.
Is there a standard sizing system for O-rings?
Yes, O-rings are commonly sized using the AS568 standard, which specifies inner diameters and cross-sectional diameters. This standard facilitates consistent identification and replacement.
Measuring O-rings accurately is essential for ensuring proper sealing and functionality in various applications. The process involves determining the O-ring’s inner diameter (ID), outer diameter (OD), and cross-sectional diameter (CS). Utilizing precise measuring tools, such as calipers or micrometers, is crucial for obtaining accurate dimensions. It is also important to consider the material and hardness of the O-ring, as these factors can influence performance and compatibility with different substances.
When measuring, it is recommended to take multiple measurements to account for any variations and ensure consistency. Additionally, understanding the specific requirements of the application, including pressure, temperature, and chemical exposure, will help in selecting the right O-ring size and material. Proper documentation of the measurements and specifications will facilitate easier procurement and replacement in the future.
mastering the technique of measuring O-rings is vital for achieving optimal sealing performance. By following best practices and utilizing the right tools, users can ensure that they select the correct O-ring sizes for their applications, thereby enhancing reliability and efficiency. This knowledge not only aids in maintenance but also contributes to the longevity of the equipment in which these O-rings are used.
Author Profile
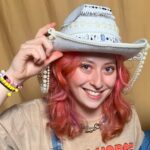
-
A designer by training, a storyteller at heart, and someone who’s always been fascinated by the quiet power of what we choose to wear.
The original Growing Jewelry collection was my attempt to bridge nature and design. I crafted rings that held real moss, asking wearers not just to display them but to care for them.
At first, it was about playfulness and poetry. But as those little green rings made their way into the world, people reached out. And the questions they asked went far beyond moss.
Because jewelry isn’t just sparkle. It’s story, symbol, and self expression and it deserves to be understood as much as admired.
So, if you’ve ever wanted to know why a ruby means passion, or how to keep your silver bright, or what your great-grandmother’s brooch might say about the era she lived in you're in the right place.
Latest entries
- April 18, 2025Investment/ValueHow Much Is a 24K Gold Ring Worth? Unveiling the True Value!
- April 18, 2025Investment/ValueWhat Factors Determine the Cost of a Platinum Ring?
- April 18, 2025MaterialsHow Can You Create Stunning Gold Filled Jewelry at Home?
- April 18, 2025Allergies/SensitivityAre Stainless Steel Earrings Safe for Sensitive Ears?