How Are Diamonds Utilized as Abrasives in Various Industries?
Diamonds are often celebrated for their breathtaking beauty and status as the ultimate symbol of love and commitment. However, these precious gemstones hold a dual identity that extends far beyond adornment. In the industrial world, diamonds are revered not just for their sparkle but for their remarkable hardness, making them an invaluable resource in the realm of abrasives. From cutting and grinding to polishing and drilling, diamonds play a pivotal role in various applications, transforming the way industries operate. In this article, we will delve into the fascinating ways diamonds are utilized as abrasives, revealing their significance in both everyday tools and advanced manufacturing processes.
The unique properties of diamonds, particularly their unparalleled hardness, allow them to outperform traditional abrasive materials. This exceptional durability enables diamonds to cut through even the toughest materials with precision and efficiency. In industrial settings, diamonds are often embedded in tools such as saw blades, grinding wheels, and drill bits, enhancing their performance and longevity. As we explore the various applications of diamond abrasives, we’ll uncover how they contribute to advancements in technology and manufacturing, driving innovation across multiple sectors.
Moreover, the versatility of diamond abrasives extends to a wide range of industries, from automotive and aerospace to electronics and construction. Their ability to produce smooth finishes and intricate designs makes them essential in processes that demand high
Applications of Diamonds as Abrasives
Diamonds are renowned not only for their beauty but also for their exceptional hardness, making them ideal for a variety of abrasive applications. They are employed in industries ranging from manufacturing to construction, providing efficient solutions for cutting, grinding, and polishing various materials.
- Cutting Tools: Diamond-tipped blades and bits are used for cutting hard materials such as stone, concrete, and metals. Their superior hardness allows for precision cuts and longer tool life compared to traditional materials.
- Grinding Wheels: Diamond grinding wheels are used in machining processes to achieve fine finishes and tight tolerances. These wheels can grind tough materials that would quickly wear down standard abrasives.
- Polishing Compounds: In jewelry making and metalworking, diamond powders serve as polishing agents. They help achieve a high-gloss finish on gemstones and metals, enhancing their aesthetic appeal.
- Coatings: Diamond coatings are applied to various tools to improve their performance and longevity. Such coatings reduce friction and wear, making tools more efficient and cost-effective.
Types of Diamond Abrasives
Diamonds are utilized in several forms, each suited to specific applications:
Type | Description | Common Applications |
---|---|---|
Natural Diamonds | Formed through geological processes, these diamonds are mined and often used in high-end tools. | Jewelry, precision cutting tools |
Synthetic Diamonds | Manufactured through high-pressure, high-temperature (HPHT) or chemical vapor deposition (CVD) methods, these diamonds are tailored for industrial use. | Grinding wheels, cutting tools, polishing compounds |
Diamond Grit | Crushed diamonds used as an abrasive material in various forms, such as powders or embedded in metal or resin. | Coated abrasives, polishing pads |
Advantages of Using Diamonds in Abrasive Applications
The use of diamonds as abrasives offers several advantages:
- Durability: Diamonds are the hardest known material, ensuring longevity and resistance to wear.
- Efficiency: They can cut and grind materials faster than traditional abrasives, improving productivity.
- Precision: Diamond abrasives provide high precision and excellent surface finishes, critical in many manufacturing processes.
- Versatility: Suitable for a wide range of applications, diamonds can effectively work on various materials, including metals, ceramics, and composites.
the unique properties of diamonds make them indispensable in abrasive applications, providing unmatched performance across numerous industries.
Applications of Diamonds in Abrasives
Diamonds are extensively utilized in various abrasive applications due to their unparalleled hardness and thermal stability. They are employed in numerous industries, including manufacturing, construction, and jewelry polishing. The unique properties of diamonds make them suitable for both industrial and precision applications.
Types of Diamond Abrasives
Diamond abrasives can be categorized based on their form and application. The main types include:
- Diamond Powders: Fine diamond particles used for grinding, polishing, and cutting applications. They are available in various grits to suit different finishing requirements.
- Diamond Wheels: These consist of a metal or resin bond that holds diamond particles, commonly used in grinding machines for shaping and finishing hard materials.
- Diamond Paste: A slurry of diamond particles in a lubricating medium, ideal for polishing and achieving high precision surfaces.
- Diamond Coated Tools: Tools coated with diamond particles, used for cutting, drilling, and machining of hard materials.
Mechanism of Action
The effectiveness of diamond abrasives stems from their mechanical properties:
- Hardness: Diamonds are the hardest known natural material, allowing them to effectively cut through or wear down other materials.
- Thermal Conductivity: Diamonds can dissipate heat generated during abrasive processes, reducing the risk of thermal damage to the workpiece.
- Chemical Inertness: Diamonds resist chemical reactions, making them suitable for use with a variety of materials, including metals, ceramics, and composites.
Industrial Uses of Diamond Abrasives
Diamond abrasives are utilized in various industrial processes, including:
Application | Description |
---|---|
Cutting | Used in saw blades for cutting stone, concrete, and metal. |
Grinding | Applied in grinding wheels for sharpening tools and finishing surfaces. |
Polishing | Employed in the final stages of surface finishing to achieve a mirror-like finish. |
Drilling | Used in drill bits for creating holes in hard materials like glass and ceramics. |
Choosing the Right Diamond Abrasive
Selecting the appropriate diamond abrasive depends on several factors:
- Material Type: Consider the hardness and properties of the material to be worked on.
- Desired Finish: The required surface finish will determine the grit size needed.
- Application Method: Whether using hand tools or machines can influence the choice of abrasive type.
- Cost Considerations: Budget constraints may affect the selection of diamond abrasives versus other materials.
The use of diamonds as abrasives showcases their versatility and effectiveness across various applications. By understanding the types, mechanisms, and appropriate selection criteria, industries can leverage diamond abrasives to enhance productivity and achieve superior results in their manufacturing and finishing processes.
Understanding the Role of Diamonds in Abrasive Applications
Dr. Emily Chen (Materials Scientist, Diamond Innovations Inc.). “Diamonds are utilized in abrasive applications due to their unparalleled hardness, which allows them to effectively cut, grind, and polish a variety of materials. Their ability to maintain sharp edges over time makes them ideal for industrial tools and processes.”
Mark Thompson (Manufacturing Engineer, Precision Tools Corp.). “In the manufacturing sector, diamond abrasives are crucial for achieving high precision in machining processes. Their unique properties enable manufacturers to enhance product quality while reducing wear on equipment, leading to significant cost savings.”
Lisa Patel (Surface Engineering Specialist, Advanced Coatings Ltd.). “The use of diamonds in abrasives extends beyond traditional applications. In modern surface engineering, diamond-coated tools are increasingly employed to improve the efficiency and longevity of cutting and grinding operations, showcasing the versatility of diamonds in various industries.”
Frequently Asked Questions (FAQs)
How are diamonds used as abrasives?
Diamonds are used as abrasives due to their exceptional hardness, making them effective for cutting, grinding, and polishing various materials, including metals, ceramics, and glass.
What industries utilize diamond abrasives?
Diamond abrasives are widely utilized in industries such as manufacturing, construction, automotive, and aerospace for applications like tool production, surface finishing, and precision machining.
What forms do diamond abrasives come in?
Diamond abrasives are available in several forms, including powders, wheels, discs, and belts, allowing for versatility in various applications and processes.
How do synthetic diamonds compare to natural diamonds in abrasives?
Synthetic diamonds are often preferred for abrasives due to their uniformity, cost-effectiveness, and ability to be engineered for specific applications, while natural diamonds are less commonly used for industrial purposes.
What are the advantages of using diamond abrasives over traditional abrasives?
Diamond abrasives offer superior cutting efficiency, longer tool life, and reduced wear on equipment compared to traditional abrasives, resulting in lower operational costs and improved productivity.
Are there any safety considerations when using diamond abrasives?
Yes, safety considerations include wearing appropriate personal protective equipment (PPE) to guard against dust and debris, ensuring proper ventilation, and following manufacturer guidelines for equipment usage to prevent accidents.
Diamonds are renowned for their exceptional hardness, making them an ideal material for abrasive applications. In various industries, diamonds are utilized in tools such as grinding wheels, cutting blades, and polishing pads. Their ability to withstand high pressure and maintain sharpness allows for efficient material removal and surface finishing across a range of substrates, including metals, ceramics, and composites.
The use of diamonds in abrasives can be categorized into two primary forms: natural diamonds and synthetic diamonds. Natural diamonds, while effective, are often more expensive and less consistent in quality compared to synthetic diamonds. The latter, produced through advanced technological processes, offer uniformity and can be tailored to specific applications, enhancing their utility in industrial settings.
Moreover, the application of diamond abrasives extends beyond traditional manufacturing. In modern technology, diamonds are increasingly used in precision machining and advanced manufacturing processes, where high accuracy and surface quality are paramount. This versatility underscores the significance of diamonds in both conventional and cutting-edge applications, reinforcing their status as a critical resource in the abrasive industry.
In summary, diamonds serve as a vital component in abrasive technology due to their unmatched hardness and durability. Their role in enhancing efficiency and precision in various applications highlights the importance of continued innovation and development in
Author Profile
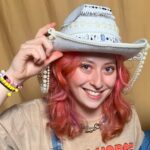
-
A designer by training, a storyteller at heart, and someone who’s always been fascinated by the quiet power of what we choose to wear.
The original Growing Jewelry collection was my attempt to bridge nature and design. I crafted rings that held real moss, asking wearers not just to display them but to care for them.
At first, it was about playfulness and poetry. But as those little green rings made their way into the world, people reached out. And the questions they asked went far beyond moss.
Because jewelry isn’t just sparkle. It’s story, symbol, and self expression and it deserves to be understood as much as admired.
So, if you’ve ever wanted to know why a ruby means passion, or how to keep your silver bright, or what your great-grandmother’s brooch might say about the era she lived in you're in the right place.
Latest entries
- April 18, 2025Investment/ValueHow Much Is a 24K Gold Ring Worth? Unveiling the True Value!
- April 18, 2025Investment/ValueWhat Factors Determine the Cost of a Platinum Ring?
- April 18, 2025MaterialsHow Can You Create Stunning Gold Filled Jewelry at Home?
- April 18, 2025Allergies/SensitivityAre Stainless Steel Earrings Safe for Sensitive Ears?